Surface Engineering by Expanded Austenite
Carburising Techniques
Modern day carburising processes are mainly gaseous processes or plasma processes, with the former being divided into atmospheric pressure carburising and low pressure carburising (LPC).
Atmospheric Pressure Carburising
Typical gaseous carburising processes involve the metal being placed in a furnace with an atmosphere containing the following gases in relatively large quantities:
The furnace atmosphere also contains smaller quantities of:
The reactions of gases and materials that produce the carburising process are as follows:
The adsorption (adhesion) of gas molecules to the steel surface
The CO molecules are dissociated (separated into smaller atoms) at higher temperature and chemical reaction of the steel surface with the C and O atoms due to the steel surface acting as a catalyst.
Diffusion of C atoms leaves O atoms on the surface of the steel. For any more carbon transfer to take place the removal of O atoms is needed. This is achieved by hydrogen atoms reacting with the oxygen to form water vapour.
Carbon monoxide also reacts with the material surface oxygen to create carbon dioxide in the atmosphere
The larger quantities of carbon dioxide and water vapour reduce the amount of diffusion reactions that can take place. Therefore the addition of methane or propane cause reactions with the carbon dioxide and the water vapour to produce carbon monoxide and hydrogen. And thus the cycle is repeated with continuing carburising.
The process in its entirety can be viewed in the figure below.
However for the case of austenitic stainless steels (ASS), this gaseous process has been found to be particularly ineffective due to the passive oxide film on the material surface acting as a barrier to the carbon atoms, meaning that diffusion cannot take place within the lattice. Therefore prior to a gaseous carburising process, a pre-treatment to activate the surface is required which results in the removal or the transformation of the oxide layer.
The advantages of this process are that there is good temperature homogeneity across the entire surface as well as good surface coverage and it allows for accurate control over the chemical potential of the carbon.
Low Pressure Carburising (LPC)
Therefore a solution was found whereby a gaseous process was implemented, but at much lower temperatures, known as low pressure carburising (LPC). At this lower temperature (< 823K) large amounts of carbon were found to dissolve in stainless steel. As no oxygen is present in the carburising gas, no internal oxidation can occur.
A major advantage of the LPC process is its ability to carburise specimens of complex geometries as well as the shorter time required for the same depth of diffusion when compared to higher temperature gaseous methods, which makes it a more economical process. The fact that the gases used are pure hydrocarbons means that the parameters are easily measured, allowing for greater control over the gas pressure, flow and temperature and so the resulting case depth and carbon content.
The reactions of the gasses differ to those during atmospheric carburising, with the carbon transfer being a product of the breakdown of the hydrocarbons; those being acetylene and propane:
The reaction are:
However prior to this treatment, as is the case with atmospheric pressure carburising, the material must be subject to oxide layer removal.
The reason that this low temperature carburising process is more effective is that the carbon atoms are far more soluble within the FCC austenitic microstructure at lower temperatures. The large quantity of carbon that can be dissolved proved to show far superior tribological properties with unaltered and in some cases improved corrosion resistance.
Plasma Process
The other commonly used modern carburising technique is that of plasma carburising ion implantation, also known as ion implantation. For this technique no surface pre-treatment is required. The process involves placing the metal this time within a vacuum furnace, which is then subject to the addition of noble gases containing hydrocarbons. Following this a DC voltage of approximately 400V – 500V is introduced between the furnace and the metal, with the metal acting as a cathode. The electric field ionises the carbon donor gases, typically methane or propane, activating them at a temperature far below the temperature required for thermal activation. This allows the carburising process to take place at a much lower temperature.
The advantages of plasma process include a faster diffusion layer formation time due to the higher chemical activity of the plasma. This combination of lower temperatures and shorter times results in smaller residual strains and little grain growth within the material. As no surface pre-treatment is needed, the process has almost no impact on the environment.
Carburising Technique Used
It is known that the carburising technique used on the samples for the investigation was that of a low temperature carburising process, however due to the patented technology, the exact details of the process cannot be released to the customer, nor can the information regarding the removal of the oxide layer or any post-treatment quenching or tempering if such treatments were applied? What is known is that every sample was carburised by a process entitled K22, with additional samples of the two nickel based alloys being subject to separate treatment entitled K33 which involved a prolonged carburisation period. This resulted in a total of 9 carburised samples to analyse.








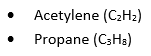
