Surface Engineering by Expanded Austenite
Discussion
At the outset of the project the aim was to investigate the microstructure, phase constituents and mechanical properties of the S-phase within the samples caused by carburisation treatments. In addition comments were to be made regarding the performance of the nickel based samples as well as regarding the effectiveness of the two different carburisation treatments.
The following discussion can be divided into threee segments:
Microstructral Behaviour
A combination of the XRD lattice expansions, surface roughness’s and carburised layer depths are all factors in the behaviour of the samples microstructures post carburisation.
It would be thought that the material which had the greatest lattice expansion would also be the material with the roughest surface, but it can be seen my comparing Tables 7 & 12, particularly focussing on the iron based alloys, that this was not the case. A reminder of these rankings for the iron based samples only is given in Table 19 below.
However it possible to qualitatively express the RST values as a function of both the XRD lattice expansions and the depth of the carburised layer which can give a more accurate ranking. As for example; a 5% lattice expansion of a thicker expanded austenite layer could be greater than that of a 10% lattice increase of a thinner layer. Therefore the use of this effective ranking removes the error associated with this situation. This relationship is expressed in equation 6 as:
Using the depth of the layer taken from the polished side and the lattice expansion from the {200} plane, selected as this plane showed the largest expansion, an effective RST ranking could be calculated. Note that as a lattice expansion value could not be ascertained for the {200} plane in sample SS 353, an estimated value was calculated by using the average ratio between the {111} plane and the {200} plane in the remaining iron based samples. This value being an expansion of 2.53%.
The resultant RST rankings of the iron alloys from high to low shown below in Table 20 better correlate with the XRD results, as it now gives a very similar ranking to the order of the XRD polished face lattice expansions. The only difference being; with the order of SS 2343 and the SS R350 sample, both of which showed to react in similar ways regarding lattice expansion and S-phase layer depth regardless.
This suggests that the iron samples which showed the greatest alteration to their microstructure as a result of carburisation are Stainless Steel 254 and Stainless Steel 832.
When subject to micro-hardness testing, the hardest of the treated iron based samples was SS 254, followed by SS 353 and SS 832. Samples 254 and 832 being particularly hard correlated with these being the two samples whose microstructure showed the greatest reaction to carburisation. The fact that sample SS 353 showed little expansion and also had a relatively thin carburised layer suggests that there is another factor aside from the expanded austenite layer which is affecting the hardness.
The optical microscopy results showed SS 353 to have a dark layer at the boundary of the expanded austenite. Further SEM analysis proved evident that a large amount of carbides were present on the top surface, explaining the increased hardness.
Sample 2343 showed an unusual reaction in term of lattice expansion, as it was the only sample to expand by a greater amount on the unpolished side. As both the surface roughness testing and the carburised layer depth analysis of SS 2343 correlated with one another, it makes this unusual lattice expansion behaviour particularly interesting. Further investigations are required to determine the reasoning for greater lattice expansion occurring on the non-polished side.
Overall it was noticed that the samples which reacted best to the carburisation treatment, that being samples SS 254 and SS 832, were the samples which had the largest atomic spacing both prior to and post carburising.
With reference to the behaviour of the iron based alloys as a whole, it was found that a thicker expanded austenite layer is formed on the unpolished side of the sample, except in the case again of SS 353 where a significant amount of carbides are thought to be present. It was also found that a larger lattice expansion took place on the polished side of the samples. Both of these phenomena’s can be contributed to the higher solubility of the non-polished, rougher face of a material.
However the less soluble polished face of the samples are seen to be significantly harder than the non-polished face, the exact cause if which was unknown. However it was thought that it could be contributed to the lesser amount strain hardening that is associated with a rougher (non-polished) surface.
Nickel Sample
It was not expected for the nickel samples to react as well as the iron based alloys to the carburising treatment due to the poor solubility of carbon in nickel. It is for this reason that they were duplicated and subjected to a separate treatment (K33). Their poor performance was confirmed throughout every investigation. The XRD, RST and carburised layer depth analysis’s all suggested that the nickel based samples were able to absorb less carbon when compared to the iron based samples.
This was further confirmed by the hardness testing which revealed only a small increase in hardness in the Inconel 617 samples and a negligible increase in the Nikrothal samples. XPS analysis delivered to show that the carbon content both at the surface and throughout the expanded austenite layer of the Inconel 617 (K33 treated) sample was significantly lower than any of the iron based samples. Their ability to dissolve carbon was so poor that it was not possible to obtain hardness depth profiles from the nickel samples due to the very thin carburised layer which was produced.
This poorer reactance when compared to the iron based samples was expected; due both to the poorer solubility of carbon in nickel and also due to the larger grain size of the nickel samples.
Although both samples reacted poorly to the carburisation process, of the two samples, Nikrothal appeared to be even less able to absorb any carbon. It consistently proved to be the worst performing material; being the softest, having the thinnest expanded austenite layer and having the smoothest surface. Instead of showing a lattice expansion due to the absorption of carbon atoms, it actually showed a decrease in atomic spacing on the polished face in two atomic planes: {200} and {220}. This was unexpected, as the fact that there was a measurable carburised layer (even though a thin one; between 3.5 µm and 5.5 µm) would suggest that some kind of lattice expansion should have occurred. Further investigations are required to explain this behaviour as it is beyond the reach of this investigation.
It is interesting to note the elemental composition of the two nickel based samples. Literature reviews revealed that the Inconel 617 samples contains approximately 54 wt% nickel, whereas Nikrothal contains about 75 wt% nickel.
The iron and chromium contents are very comparable. This higher nickel content found in Nikrothal explains why the carburisation process was less effective when compared to its counterpart nickel material, as carbon has a poor ability to be absorbed within nickel.
Further reasoning for this could be the higher molybdenum and cobalt weight percentage found in Inconel 617 and the presence of silicon in Nikrothal shown in Table 21 below.
Molybdenum atoms are known to be larger than any of the other elements which are part of the alloy, therefore it is likely that the atomic spacing in the material with the greater amount of molybdenum (Inconel 617) will be larger, as so more trap sites for carbon are created. As prior stated, it was witnessed that materials with larger atomic spacing when untreated tended to react better to carburisation. Molybdenum is also known to have an extremely high affinity to carbon. Therefore the molybdenum content could also be factor in the difference between the two materials capacity to absorb carbon.
The higher weight percentage of cobalt in Inconel 617 could also be a factor for the more effective case hardening, however this is more unlikely due to the relatively inert properties of cobalt. Further research is required to determine which of the three elements discussed (nickel, molybdenum and cobalt) had a greater effect on a materials capability to be case hardening via low temperature carburisation.
Silicon is known to have an even poorer affinity to carbon than nickel does. Therefore its presence, even though only thought to be approximately 1.5%, could have an effect on the seemingly low carbon diffusion capabilities of Nikrothal.
K22 Vs K33 Carburisation Treatment
When comparing the K22 and K33 carburisation processes, the results witnessed were unexpected. It was known that the K33 treatment was of an increased time temperature regime, therefore suggesting that the K33 treated samples would have absorbed more carbon. This was proved not to be the case in the case in the majority of the investigations.
When examining the XRD results, the K22 treated nickel samples both showed a greater lattice expansion compared to the K33 treated samples. The K33 treated samples were also harder than their K22 counterparts. Only in select cases did the K33 treated Nikrothal samples react ‘better’ than the K22 treated samples. One of these cases bein;g in terms of surface roughness, the other being in terms of the depth of the carburised layer. However these differences between the K22 and K33 treatments were insignificant in magnitude.
The exact reasoning for the K33 treatment appearing less effective is unknown. One reason could perhaps be; that for the temperature that the process was carried out at, the saturation limit of the amount of carbon that could be dissolved was reached. Further investigations and more knowledge of the details of the treatments are required before any definite reasoning regarding the effectiveness of the processes can be stated.


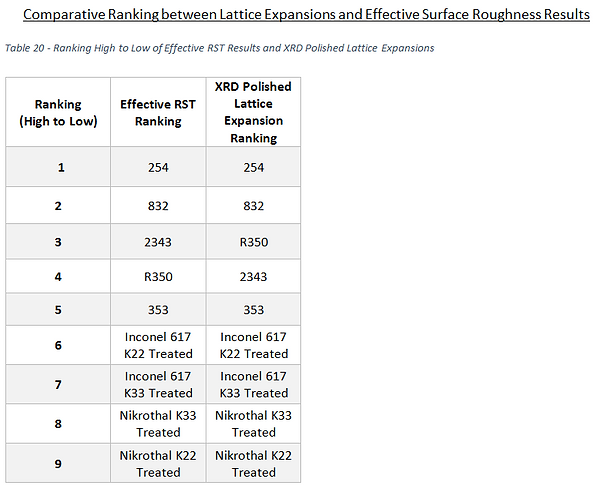
