Surface Engineering by Expanded Austenite
Micro-Hardness Analysis
Surface Hardness Testing
The surface hardness tests were carried out in order to give three different comparisons, those being:
-
A comparison between the hardness of each material
-
A comparison of increase in hardness of each material due to carburisation
-
A comparison of the effectiveness of the K22 and K33 carburising treatments
Surface Hardness of Untreated Sample
Analysing the polished face of the untreated samples showed that initially the hardest material was Inconel 617, with an average Vickers Hardness value of 253HV. The material with the lowest hardness value (177HV) was the 832 stainless steel sample. Hardness values for all of the samples can be found in the table below.
Ranking High to Low of Polished Face Surface Hardness Values Prior to Carburisation
Surface Hardness of Treated Samples
When examining the surface hardness values of the carburised samples, the effectiveness of the process can be truly appreciated. The ranking bears no resemblance to that of untreated table, with the HV values being in the region of 4 to 8 times higher for the iron based samples. This confirms the XRD conclusions of the iron based samples being a lot more receptive to the carburising treatment than the nickel samples.
The ranking of the hardness of the samples also matched the XRD lattice expansions on the polished face, with the exception of SS 353. SS 353 showed the lowest expansion of all the iron based samples and was also by far the smoothest of the iron samples. However it has the 2nd highest hardness value. This again suggests that there is another influence affecting this sample. It would not be expected that a material with a low roughness and small lattice expansion to be one of the hardest samples. One reason for this could be the formation of a precipitate on the surface, such as chromium carbides, that was not discovered during the XRD analysis due to the distorted nature of the 2nd austenite peak. A further transmission electron microscope (TEM) analysis is required of this sample to reveal the nature of its microstructure, but unfortunately due to equipment maintenance, this would not be possible for this particular investigation.
The surface hardness results also acted to confirm the poor reaction of the nickel based alloys to the carburising treatment, with the surface hardness values of the Inconel 617 samples only approximately doubling. In the case of the Nikrothal samples, the changes in hardness were insignificant, also correlating with the low roughness and surprising contraction witnessed in the XRD analysis.
Ranking of Average Surface Hardness Post Carburisation
K22 and K33 Treatment Comparison
In terms of the effectiveness of the carburisation treatments it is hard to draw many conclusions in terms of comparing the K22 and K33 process, due to the poor way in which the nickel samples responded to both treatments.
Once again the Inconel 617 samples performed better than the Nikrothal samples, with the Vickers hardness of Inconel 617 doubling in magnitude compared to the insignificant increase measured in the Nikrothal sample. So when only taking into account the Inconel 617 sample, the K22 treatment appeared to be the more effective one, with the HV value being 33HVs greater than the K33 treated sample. Although this was not expected, with the K33 process being of a longer treatment time, it is consistent with the results seen in the XRD and RST investigations so far.
Hardness Depth Profiling
Two depth hardness profiles were taken from the cross section of each sample; one starting from the polished face and one starting from the non-polished face. This was to further investigate the effect which preparing the samples had on the diffusion of carbon within the material. The resulting profiles should show a decaying exponential graph, with the maximum hardness being found at the surface, shown in Figures 50 – 54 below.
All nickel samples (both K22 and K33) have been excluded from the micro-hardness depth profiling, as it can be seen from Figures 33, 34, 36 & 37 that the micro-hardness indentations have missed the carburised layer due to its shallow nature and the indents cannot be made any closer to the surface.
Micro-Hardness Depth Profiling Results
The nature of the graphs shape were decaying exponential as predicted and with every graph, the results are clear that the unpolished depth layer starts softer than the polished side by a fairly significant amount, with some being almost half as hard. However the gradient of the unpolished side is more gradual and the hardness levels off deeper into the sample. It can also be seen that at a certain depth (approximately between 15 µm and 35 µm) the line of the graphs often cross, meaning that the hardness value on the unpolished side becomes greater. This can be described by the deeper carburised layer causing an increase in number of dislocations deeper within the sample. The presence of these dislocations introduce strain and the resultant strain hardening, as well as create a paths for the dissolution of more carbon which allows for more hardening via solid solution hardening. These findings are matched by those in Maistro et al.
The fact that the unpolished sides were harder, deeper within the samples correlated with the optical microscopy analysis that also showed the unpolished sides to have a thicker modified layer.
The unpolished side is seen to have a lower maximum hardness, however the exact reasoning for this in unknown. One possibility is that the rougher nature of the non-polished surface is known to relax residual stresses at the outside surface. This in turn means a reduction in hardness with there being less strain hardening.
Micro-Hardness Testing Summary
Post carburising, the iron based samples were found to be within the region of 4 – 8 times harder than they were before treatment, with the hardest samples being SS 254 and SS 353. It was unexpected for SS 353 to have such a high hardness value due to its low roughness and relatively thin expanded austenite layer.
The hardness of nickel sample Inconel 617 showed little modifications, with the Nikrothal samples showing almost no increase in hardness at all. Although insignificant, the K22 treatment appeared to be more effective in the Inconel 617 sample.
As a result of the very thin expanded austenite layer, a hardness profiles were not able to be obtained from the nickel samples.
A higher peak hardness was found on the surface of the polished face of the samples. However the non-polished surfaces, although having a lower HV value, had a deeper, more homogenous distribution of carbon throughout the S-phase.




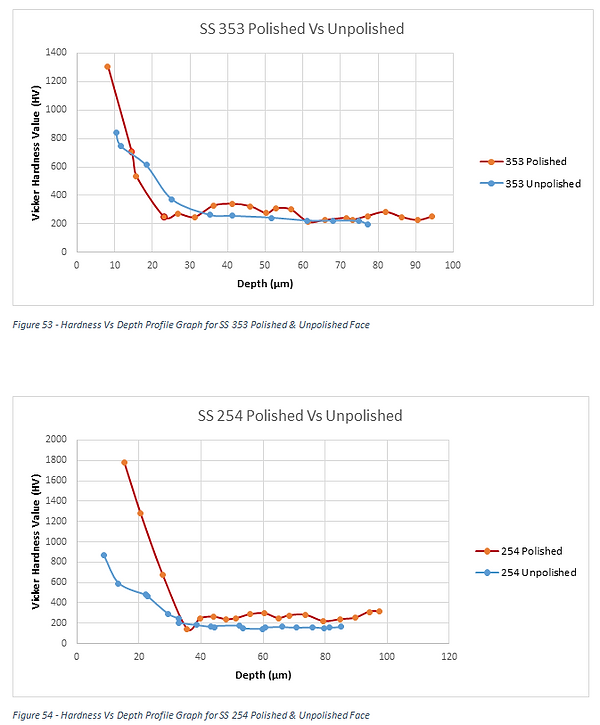